انواع گازهای مورد استفاده در کپسول هوابرش
فرآیند هوا برش (Oxy-Fuel Cutting)، که یکی از قدیمیترین و پرکاربردترین روشهای برش حرارتی فلزات است، بر پایه واکنش شیمیایی اکسیداسیون فلز و همچنین ذوب و بیرون راندن مواد مذاب بنا شده است. قلب تپنده این فرآیند، گازهایی هستند که با دقت و در نسبتهای مشخصی ترکیب و مشتعل میشوند. انتخاب صحیح این گازها نه تنها بر کیفیت و سرعت برش تأثیر مستقیم دارد، بلکه نقش حیاتی در ایمنی اپراتور و هزینههای عملیاتی ایفا میکند.
در این مقاله جامع، به بررسی عمیق انواع گازهای مورد استفاده در کپسول هوا برش میپردازیم. از نقش محوری اکسیژن خالص به عنوان گاز اکسید کننده گرفته تا انواع گازهای سوختی رایج مانند استیلن، پروپان، متان و هیدروژن، و حتی گازهایی که ممکن است به اشتباه یا در فرآیندهای مرتبط مطرح شوند. هدف ما ارائه اطلاعات دقیق، کاربردی و قابل اعتماد است تا شما بتوانید بهترین انتخاب را برای نیازهای برش خود داشته باشید.
اهمیت انتخاب گاز مورد استفاده در کپسول هوا برش و نقش گاز در عملکرد دستگاه
در فرآیند هوابرش انتخاب گاز مناسب تأثیر مستقیمی بر کیفیت برش، سرعت عملیات، ایمنی اپراتور و هزینههای پروژه دارد. پیش از بررسی بیشتر نقش این گاز به عوامل کلیدی موثر بر این انتخاب میپردازیم:
عوامل کلیدی در انتخاب گاز
گازها در هوا برش دو نقش اصلی دارند: تولید حرارت برای گرم کردن فلز تا دمای واکنش (معمولاً 870-980 درجه سانتیگراد برای فولاد کربنی) و ایجاد واکنش اکسیداسیون برای حذف فلز مذاب از محل برش. انتخاب نادرست گاز میتواند منجر به مشکلاتی مانند برش ناقص، تولید سرباره زیاد، افزایش مصرف انرژی یا خطرات ایمنی مانند نشتی گاز یا انفجار شود.
- نوع فلز: فلزات آهنی (مانند فولاد کربنی یا کمآلیاژ) با اکسیژن و گازهای سوختی مانند استیلن به خوبی برش میخورند، اما فلزات غیرآهنی (مانند آلومینیوم یا مس) ممکن است نیاز به گازهای خاص مانند آرگون داشته باشند. (البته برای برش این فلزات معمولا از پلاسما کاتینگ یا لیزر کاتینگ استفاده میشود)
- ضخامت فلز: فلزات ضخیمتر (بیش از 50 میلیمتر) نیاز به گازهایی با دمای شعله بالا مانند استیلن دارند، در حالی که فلزات نازکتر (کمتر از 20 میلیمتر) با پروپان یا متان به خوبی برش میخورند.
- هزینه: گازهای ارزانتر مانند پروپان و متان برای پروژههای بزرگ و اقتصادی مناسبترند، در حالی که استیلن و هیدروژن هزینههای بالاتری دارند.
- ایمنی: گازهایی مانند استیلن به دلیل ناپایداری شیمیایی نیاز به رعایت استانداردهای ایمنی سختگیرانه دارند.
- تجهیزات: مشعلها، نازلها و رگولاتورهای فشار باید با نوع گاز انتخابشده سازگار باشند.
- شرایط محیطی: در محیطهای با تهویه ضعیف، استفاده از گازهای ایمنتر مانند پروپان توصیه میشود.
برای مثال، استفاده از استیلن برای برش فولاد ضخیم به دلیل دمای شعله بالا (حدود 3100 درجه سانتیگراد) بسیار مؤثر است، اما هزینه بالای آن ممکن است برای پروژههای کوچک مقرونبهصرفه نباشد. در مقابل، پروپان با هزینه کمتر و دمای شعله پایینتر (حدود 2800 درجه سانتیگراد) برای برش فلزات نازکتر مناسب است.
جدول 1: عوامل تاثیرگذار بر انتخاب گاز در هوابرش
عامل | توضیح |
نوع فلز | فلزات آهنی با اکسیژن و استیلن برش میخورند؛ فلزات غیرآهنی نیاز به هیدروژن یا آرگون دارند. |
ضخامت فلز | فلزات ضخیمتر نیاز به دمای شعله بالاتر دارند (استیلن)؛ فلزات نازکتر با پروپان یا متان برش میخورند. |
هزینه | پروپان و متان اقتصادیترند؛ استیلن و هیدروژن هزینه بالاتری دارند. |
ایمنی | استیلن و هیدروژن نیاز به رعایت استانداردهای ایمنی سختگیرانه دارند. |
تجهیزات | مشعلها و نازلها باید با نوع گاز سازگار باشند. |
شرایط محیطی | در محیطهای با تهویه ضعیف، گازهای ایمنتر مانند پروپان مناسبترند. |
بنابراین، انتخاب گاز مناسب فراتر از پر کردن کپسول است. این یک تصمیم مهندسی است که باید با در نظر گرفتن نوع ماده، ضخامت، کیفیت مورد نظر، سرعت برش، هزینههای عملیاتی و مهمتر از همه، ملاحظات ایمنی انجام شود.
گازهای اکسید کننده در فرآیند هوابرش
اکسیژن خالص (O₂) مهمترین گاز اکسید کننده در فرآیند هوابرش است. این گاز با خلوص بالا (معمولاً 99.5٪ یا بیشتر) برای ایجاد واکنش اکسیداسیون با فلز داغ استفاده میشود. در فرآیند هوا برش، فلز ابتدا با شعله گاز سوختی تا دمای واکنش (870-980 درجه سانتیگراد برای فولاد) گرم میشود. سپس جریان متمرکز اکسیژن باعث اکسید شدن فلز و تشکیل اکسید فلزی (مانند FeO یا Fe₂O₃) میشود که به صورت سرباره از محل برش خارج میگردد.
ویژگیها و مزایای اکسیژن خالص
خلوص گاز اکسیژن در هوا برش بسیار اهمیت دارد. ناخالصیهایی مانند نیتروژن یا آرگون دمای شعله را کاهش داده و سرعت واکنش اکسیداسیون را کم میکنند، که منجر به کاهش سرعت برش، افزایش مصرف گاز، کیفیت پایینتر برش و تولید سرباره بیشتر میشود. مزایا و ویژگیهای اکسیژن که به فرآیند هوابرش کمک میکنند عبارتند از:
- دمای بالا: در ترکیب با استیلن، دمای شعله تا 6000 درجه سانتیگراد میرسد، که برای برش فلزات آهنی ایدهآل است.
- سرعت برش بالا: جریان اکسیژن متمرکز، فلز مذاب را به سرعت از محل برش حذف میکند.
- کیفیت برش: تولید برشهای تمیز با حداقل سرباره و اعوجاج (تغییر شکل فلز).
- کاربرد گسترده: مناسب برای برش فولاد کربنی، فولاد کمآلیاژ و برخی فلزات دیگر.
دقت کنید که اکسیژن خالص قابل اشتعال نیست، اما به شدت از احتراق پشتیبانی میکند. تماس با روغن، گریس یا مواد قابل اشتعال میتواند باعث انفجار شود. کپسولهای اکسیژن باید در فشار ایمن (معمولا تا 200 بار) و در محیطی خنک، خشک و دور از منابع حرارتی نگهداری شوند. همچنین استفاده از رگولاتورهای فشار مناسب و بررسی منظم شیلنگها برای جلوگیری از نشتی ضروری است.
کاربردهای خاص
اکسیژن خالص در برش فلزات آهنی مانند فولاد کربنی و کمآلیاژ بسیار مؤثر است. برای مثال، در کارخانههای فولادسازی، اکسیژن برای برش شمشهای فولادی با ضخامت بالا استفاده میشود. اما برای فلزات غیرآهنی مانند آلومینیوم یا مس، که به دمای ذوب بالاتری نیاز دارند یا با اکسیژن واکنش نمیدهند، فرآیندهای جایگزین مانند برش پلاسما مناسبترند.
جدول 2: مشخصات اکسیژن در هوابرش
ویژگی | توضیح |
خلوص | ≥99.5٪ |
دمای شعله (با استیلن) | تا 6000 درجه سانتیگراد |
کاربرد اصلی | برش فلزات آهنی (فولاد کربنی، فولاد کمآلیاژ) |
نکات ایمنی | جلوگیری از تماس با مواد قابل اشتعال، ذخیرهسازی در فشار ایمن |
باید اضافه کرد که اکسیژن صنعتی معمولا از طریق فرآیند تقطیر جزء به جزء هوای مایع تولید میشود. اکسیژن را میتوان به صورت فشرده در سیلندرها (کپسولها) یا به صورت مایع در تانکرهای کرایوژنیک (بسیار سرد) ذخیره کرد. ذخیرهسازی مایع برای مصرفکنندگان با حجم بالا اقتصادیتر است، زیرا حجم بیشتری از گاز را در فضای کمتر ذخیره میکند.
گازهای سوختی مورد استفاده در سیستمهای هوابرش
گازهای سوختی برای تولید حرارت اولیه و گرم کردن فلز تا دمای واکنش با اکسیژن استفاده میشوند. انتخاب گاز سوختی به عواملی مانند ضخامت فلز، هزینه، دسترسی و تجهیزات بستگی دارد. در ادامه، چهار گاز سوختی رایج بررسی میشوند:
1.استیلن (C₂H₂)
گاز استیلن پرکاربردترین گاز سوختی در هوابرش است و این گاز به دلیل دمای شعله بالا و سرعت احتراق سریع، برای برش فلزات ضخیم و جوشکاری بسیار مناسب است. استیلن، گازی بیرنگ و با بوی سیر مانند در حالت ناخالص است. مهمترین ویژگی آن تولید بالاترین دمای شعله در میان گازهای سوختی رایج هنگام ترکیب با اکسیژن (حدود 3100 تا 3300 درجه سانتیگراد) است. این دمای بالا باعث پیشگرمایش بسیار سریع میشود. شعله استیلن-اکسیژن بسیار متمرکز است.
مزایا
- دمای شعله بالا (3100 درجه سانتیگراد در ترکیب با اکسیژن).
- برش سریع و تمیز با حداقل سرباره.
- مناسب برای فولاد کربنی با ضخامت بیش از 50 میلیمتر.
معایب
- هزینه بالا نسبت به سایر گازها.
- ناپایداری شیمیایی (نیاز به کپسولهای مخصوص با مواد جاذب مانند استون).
- حساسیت به فشار بالا (بیش از 1.5 بار ممکن است خطرناک باشد).
استیلن در پروژههای صنعتی سنگین مانند برش صفحات فولادی ضخیم در کشتیسازی، ساخت پلها یا کارخانههای فولادسازی استفاده میشود. همچنین در جوشکاری اکسیاستیلن (oxy-acetylene welding) کاربرد گستردهای دارد. برای مثال، در ساخت شاسی کشتیها، استیلن برای برش دقیق صفحات فولادی با ضخامت 100-300 میلیمتر استفاده میشود.
2.پروپان (C₃H₈)
پروپان به دلیل هزینه پایین و دسترسی آسان، جایگزین محبوبی برای استیلن است. این گاز برای برش فلزات نازکتر و پروژههای اقتصادی مناسب است. پروپان، گازی بیرنگ و بیبو است که برای شناسایی نشت به آن مواد بودار اضافه میشود. دمای شعله آن با اکسیژن (حدود 2800 تا 2900 درجه سانتیگراد) کمتر از استیلن است، اما محتوای حرارتی کل (BTU/ واحد حجم در حالت مایع) آن بالاتر است. شعله پروپان-اکسیژن گستردهتر از شعله استیلن است.
مزایا
- هزینه کمتر نسبت به استیلن.
- ایمنی بالاتر به دلیل پایداری شیمیایی.
- مناسب برای برش فولاد نازک (تا 50 میلیمتر).
معایب
- دمای شعله پایینتر (2800 درجه سانتیگراد).
- تولید سرباره بیشتر نسبت به استیلن.
- نیاز به نازلهای خاص برای بهینهسازی شعله.
پروپان در کارگاههای کوچک، تعمیرات خودرو، و پروژههای ساختوساز سبک استفاده میشود. برای مثال، در تعمیر بدنه خودرو، پروپان برای برش ورقهای نازک فولادی (5-20 میلیمتر) به کار میرود.
3.متان (CH₄)
متان (گاز طبیعی) در برخی کاربردهای خاص استفاده میشود. دمای شعله آن پایینتر از استیلن و پروپان است، بنابراین برای برش فلزات نازک یا در مناطقی با دسترسی آسان به گاز طبیعی مناسب است. این گاز ارزانترین گاز سوختی در میان گزینههای رایج است، به خصوص اگر به صورت لولهکشی در دسترس باشد. دمای شعله آن با اکسیژن (حدود 2700 تا 2800 درجه سانتیگراد) پایینترین در میان گازهای سوختی اصلی است.
مزایا
- هزینه بسیار پایین.
- دسترسی آسان در مناطق صنعتی با خطوط گاز طبیعی.
معایب
- دمای شعله پایین (2700 درجه سانتیگراد).
- سرعت برش کمتر.
- نیاز به مشعلهای خاص.
متان در کارخانههای صنعتی بزرگ که به خطوط گاز طبیعی دسترسی دارند، برای برش ورقهای نازک (زیر 10 میلیمتر) استفاده میشود. (البته متان معمولا برای برش فلزات به کار نمیرود، چون دمای آن کافی نیست. این گاز بیشتر برای پیشگرمایش یا حرارتدهی سطحی کاربرد دارد.)
4.هیدروژن (H₂)
هیدروژن به دلیل شعله تمیز و دمای بالا در کاربردهای خاص، استفاده میشود. هیدروژن، گازی بیرنگ، بیبو و بسیار سبک است. دمای شعله آن با اکسیژن (حدود 2800 تا 3000 درجه سانتیگراد) بالاست، اما انرژی تابشی شعله آن کمتر از استیلن است.
مزایا
- شعله تمیز و بدون دود.
- مناسب برای فلزات حساس به اکسیداسیون.
معایب
- هزینه بالا.
- خطرات ایمنی به دلیل اشتعالپذیری بالا.
- نیاز به تجهیزات تخصصی.
هیدروژن در صنایع هوافضا و برش فلزات غیرآهنی که نیاز به سطح برش تمیز دارند، استفاده میشود. برای مثال، در تولید قطعات آلومینیومی هواپیما، هیدروژن برای برش دقیق استفاده میشود.
جدول 3: مقایسه گازهای سوختی در هوابرش
گاز | دمای شعله (°C) | هزینه | ایمنی | کاربرد اصلی |
استیلن | 3100 | بالا | متوسط | برش فلزات ضخیم |
پروپان | 2800 | پایین | بالا | برش فلزات نازک |
متان | 2700 | خیلی پایین | بالا | کاربردهای خاص |
هیدروژن | 2800 | بالا | پایین | برش فلزات غیرآهنی |
در نتیجه انتخاب گاز سوختی تأثیر قابل توجهی بر دمای شعله، سرعت پیشگرمایش، پروفیل حرارتی شعله و در نهایت سرعت و کیفیت برش دارد.
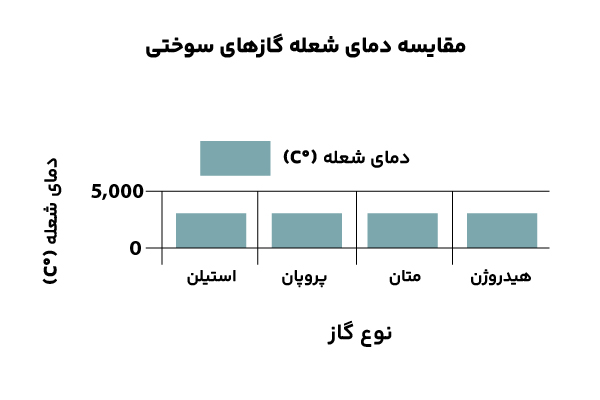
تجهیزات هوا برش و سازگاری با گازها
تجهیزات هوا برش شامل مشعل، نازل، رگولاتور فشار، شیلنگها و کپسولهای گاز است. سازگاری این تجهیزات با گازهای مختلف برای عملکرد بهینه و ایمنی حیاتی است.
1. مشعل (Torch)
مشعل قلب سیستم هوابرش است که گاز سوختی و اکسیژن را مخلوط کرده و شعله را تولید میکند. مشعلها برای گازهای خاص طراحی میشوند:
- مشعلهای استیلن: دارای نازلهای کوچک و متمرکز برای تولید شعله با دمای بالا.
- مشعلهای پروپان: نیاز به نازلهایی با منافذ بزرگتر برای جبران دمای پایینتر شعله.
- مشعلهای هیدروژن: به دلیل اشتعالپذیری بالا، نیاز به طراحی ایمنتر با سیستمهای خنککننده دارند.
- مشعلهای متان: معمولا برای کاربردهای صنعتی خاص طراحی شده و با خطوط گاز طبیعی سازگارند.
شیرهای تنظیم جریان روی مشعل میز به اپراتور امکان میدهند تا نسبت اختلاط اکسیژن و گاز سوختی برای شعله پیشگرم و همچنین جریان جت اکسیژن برش را تنظیم کند.
2. نازلها
نازلها جریان گاز را تنظیم کرده و شکل شعله را تعیین میکنند. هر گاز نیاز به نازل مخصوص دارد:
- نازلهای استیلن: کوچک و متمرکز برای شعله داغ و دقیق.
- نازلهای پروپان و متان: منافذ بزرگتر برای جریان گاز بیشتر.
- نازلهای هیدروژن: طراحی شده برای شعله تمیز و ایمنی بالا.
ضمن اینکه باید اطمینان حاصل کرد که نازل انتخابی از نظر اندازه و نوع (پیچی، سری) با مشعل مورد استفاده سازگار است.
3. رگولاتورهای فشار
رگولاتورها یکی از حیاتیترین تجهیزات از نظر سازگاری با گاز هستند. وظیفه اصلی رگولاتور، کاهش فشار بسیار بالای گاز در سیلندر به فشار کاری ایمن و پایدار مورد نیاز برای مشعل است. این فشار کاری برای هر گاز متفاوت است:
- استیلن: 0.5-1.5 بار (فشار بالاتر خطرناک است).
- پروپان: 1-4 بار.
- هیدروژن: 1-3 بار.
- اکسیژن: 2-10 بار بسته به ضخامت فلز.
همیشه باید از رگولاتوری که به طور واضح برای گاز مورد استفاده و برای محدوده فشار کاری مورد نیاز در کاربرد خاص شما طراحی و نشانهگذاری شده است، استفاده کنید.
4.شیلنگها و اتصالات
شیلنگها باید با گازها سازگار باشند تا دچار فرسودگی شیمیایی نشوند و بتوانند فشار کاری لازم را تحمل کنند:
- شیلنگهای استیلن: مقاوم به حلالهای شیمیایی مانند استون.
- شیلنگهای پروپان و متان: استاندارد و مقاوم به فشار.
- شیلنگهای هیدروژن: مقاوم به نشتی برای جلوگیری از خطرات.
درکل شیلنگهای مخصوص برش و جوشکاری معمولا از لاستیک تقویت شده یا مواد مصنوعی ساخته میشوند که در برابر سایش، حرارت و فشار مقاوم هستند.
5.کپسولهای گاز
اگرچه سیلندرها مستقیما سازگاری با فرآیند برش ندارند، اما طراحی و مشخصات آنها برای ذخیرهسازی ایمن گازهای مختلف حیاتی است:
- کپسولهای استیلن: حاوی مواد جاذب (مانند استون) برای جلوگیری از انفجار.
- کپسولهای پروپان و متان: سادهتر و ارزانتر.
- کپسولهای هیدروژن: نیاز به طراحی خاص برای جلوگیری از نشتی.
- کپسولهای اکسیژن: مقاوم به فشار بالا (تا 200 بار).
شیرهای روی سیلندرهای گازهای مختلف نیز دارای طراحی اتصال متفاوتی هستند (رزوهها، جهت رزوهها، اندازه). این تفاوت عمدی است و به عنوان یک ویژگی ایمنی برای جلوگیری از اتصال تصادفی رگولاتور یک گاز به سیلندر گاز دیگر طراحی شده است.
جدول 4: سازگاری تجهیزات هوا برش با گازها
تجهیزات | استیلن | پروپان | هیدروژن |
مشعل | نازل متمرکز | نازل با منافذ بزرگ | نازل ایمن |
رگولاتور فشار | 0.5-1.5 بار | 1-4 بار | 1-3 بار |
شیلنگ | مقاوم به استون | استاندارد | مقاوم به نشتی |
کپسول | حاوی مواد جاذب | استاندارد | طراحی خاص |
توجه داشته باشید که عدم سازگاری تجهیزات با گازها نه تنها باعث عملکرد ضعیف میشود، بلکه میتواند عواقب ایمنی بسیار جدی و جبرانناپذیری داشته باشد. استفاده از رگولاتور یا شیلنگ نامناسب میتواند منجر به نشت گاز، آتشسوزی یا انفجار شود. استفاده از نازل اشتباه میتواند باعث پسسوزی مکرر یا فلاشبک شود.
گازهای محافظ و کمکی در فرآیند هوابرش
گازهای محافظ و کمکی برای بهبود کیفیت برش، کاهش اکسیداسیون و افزایش ایمنی استفاده میشوند. این گازها بیشتر در فرآیندهای پیشرفته مانند برش پلاسما یا هوا برش دقیق کاربرد دارند.
1.نیتروژن (N₂)
نیتروژن به دلیل خاصیت خنثی بودن، از اکسیداسیون فلز جلوگیری کرده و کیفیت برش را بهبود میبخشد. همچنین در دماهای بالا میتواند با برخی فلزات واکنش نشان دهد (نیتروژندهی).
مزایا
- کاهش اکسیداسیون و تولید برش تمیز.
- ایمنی بالا به دلیل غیرفعال بودن.
معایب
- هزینه بالاتر نسبت به گازهای سوختی.
- نیاز به تجهیزات خاص.
نیتروژن در برش پلاسما و برش فولاد ضدزنگ استفاده میشود. همچنین در برش لیزر به عنوان گاز کمکی برای برش بدون اکسیداسیون کاربرد دارد. برای مثال، در تولید قطعات صنعتی دقیق، نیتروژن برای جلوگیری از تغییر رنگ سطح فولاد ضد زنگ استفاده میشود.
2.آرگون (Ar)
آرگون به دلیل خنثی بودن، در برش فلزات غیرآهنی مانند آلومینیوم و مس استفاده میشود. در واقع گاز آرگون یک گاز محافظ اصلی و پرکاربرد در جوشکاری TIG و MIG است. گاز سنگینتر کاملاًبیاثر است و در دماهای جوشکاری با فلزات واکنش نمیدهد.
مزایا
- ایجاد محیط غیرفعال و کاهش واکنشهای شیمیایی.
- بهبود کیفیت سطح برش.
معایب
- هزینه بالا.
- کاربرد محدود در هوابرش سنتی.
آرگون در برش پلاسما و کاربردهای دقیق مانند صنایع هوافضا استفاده میشود. برای مثال، در تولید قطعات آلومینیومی هواپیما، آرگون برای برش تمیز و بدون اکسیداسیون به کار میرود.
3.دیاکسید کربن (CO₂)
گازی نسبتا بیاثر است، اما در دماهای بالا میتواند تجزیه شده و اکسیژن تولید کند که میتواند بر فرآیند تأثیر بگذارد (به همین دلیل در جوشکاری MIG با فولاد کربنی مناسب است اما برای جوشکاری TIG یا مواد خاص کمتر استفاده میشود.)
مزایا
- هزینه پایین و دسترسی آسان.
- بهبود پایداری شعله.
معایب
- ممکن است باعث اکسیداسیون در فلزات حساس شود.
- کاربرد محدود در هوابرش سنتی.
دیاکسید کربن در جوشکاری MIG/MAG به عنوان گاز محافظ یا بخشی از مخلوط گاز محافظ استفاده میشود (معمولاً با آرگون مخلوط میشود). همچنین در برخی کاربردهای برش لیزر و پلاسما نیز به کار میرود.
جدول 5: مقایسه گازهای محافظ و کمکی
گاز | کاربرد اصلی | مزایا | معایب |
نیتروژن | برش پلاسما، کاهش اکسیداسیون | برش تمیز، ایمنی بالا | هزینه بالا، نیاز به تجهیزات |
آرگون | برش فلزات غیرآهنی | محیط غیرفعال، کیفیت بالا | هزینه بالا |
دیاکسید کربن | جوشکاری و برخی برشها | هزینه پایین، دسترسی آسان | احتمال اکسیداسیون |
در نهایت باید اضافه کرد که مهم است که، اگرچه نیتروژن، آرگون و دی اکسید کربن گازهای مهمی در دنیای برش و جوش حرارتی هستند، اما آنها جزء سیستم گاز مورد نیاز برای عملکرد استاندارد فرآیند هوا برش نیستند. فرآیند هوا برش فقط به اکسیژن خالص و یک گاز سوختی نیاز دارد. هرگونه استفاده از گازهای دیگر در سیستمهای مرتبط باید با دانش و هدف مشخص انجام شود.
عوامل دیگری که در انتخاب گاز تاثیر دارند (فراتر از نوع گاز)
علاوه بر نوع گاز، عوامل دیگری نیز وجود دارند که در فرآیند هوا برش و انتخاب تجهیزات تأثیرگذارند:
- فشار گاز: فشار کاری گاز سوختی و اکسیژن برای عملکرد صحیح مشعل و برش با کیفیت حیاتی است. رگولاتورها وظیفه کاهش فشار بالای داخل سیلندر به فشار کاری مورد نیاز را بر عهده دارند. فشارهای نامناسب میتوانند منجر به شعله ناپایدار، برش ناقص، پسسوزی یا فلاشبک شوند.
- نرخ جریان (Flow Rate): حجم گاز مصرفی در واحد زمان، که به اندازه نازل مشعل و ضخامت ماده در حال برش بستگی دارد. مشعلها و رگولاتورها باید قادر به تأمین نرخ جریان مورد نیاز باشند.
- اندازه و نوع مشعل (Torch) : مشعلهای هوا برش انواع مختلفی دارند (مانند نوع انژکتوری و نوع فشار برابر) که برای استفاده با گازهای سوختی خاص و فشارهای کاری متفاوت طراحی شدهاند. اندازه نازل مشعل نیز باید متناسب با ضخامت ماده و نوع گاز باشد.
- وضعیت تجهیزات: شیلنگها، رگولاتورها، شیرها و مشعلها باید در شرایط کاری ایمن و مناسب باشند. تجهیزات آسیبدیده یا فرسوده میتوانند باعث نشت گاز، شعله ناپایدار و حوادث ایمنی شوند.
- دمای محیط: دمای محیط میتواند بر فشار داخل سیلندرها و همچنین عملکرد رگولاتورها تأثیر بگذارد. در دماهای بسیار پایین، ممکن است خروج گاز از سیلندر های پروپان دشوار شود.
- تهویه محیط کار: کار با گازهای سوختی و اکسیژن، همچنین تولید دود و گازهای ناشی از برش، نیازمند تهویه مناسب محیط کار برای جلوگیری از تجمع گازها و حفظ سلامت اپراتور است.
همچنین هزینه گازها بخش قابل توجهی از هزینه عملیاتی در فرآیند هوا برش را تشکیل میدهد. هنگام انتخاب گاز، نباید فقط قیمت واحد هر متر مکعب گاز را در نظر گرفت، بلکه باید عواملی مانند سرعت و کیفیت برش، مصرف گاز در واحد زمان و هزینه اجاره/نگهداری سیلندر را نیز مدنظر قرار داد. تحلیل هزینه-فایده با در نظر گرفتن تمامی این عوامل برای انتخاب اقتصادیترین گاز سوختی برای یک کاربرد خاص ضروری است.
نتیجهگیری
انتخاب گاز مناسب در فرآیند هوابرش به عوامل متعددی مانند نوع فلز، ضخامت، بودجه، ایمنی و تجهیزات بستگی دارد. اکسیژن خالص به عنوان گاز اکسید کننده اصلی، نقش کلیدی در ایجاد واکنش برش دارد. استیلن برای برش فلزات ضخیم و پروپان برای پروژههای اقتصادی مناسب هستند، در حالی که متان و هیدروژن در کاربردهای خاص استفاده میشوند. گازهای محافظ مانند نیتروژن و آرگون کیفیت برش را بهبود میبخشند و در فرآیندهای پیشرفتهتر کاربرد دارند. تجهیزات هوا برش، از جمله مشعلها، نازلها و رگولاتورها، باید با نوع گاز سازگار باشند تا عملکرد بهینه و ایمنی تضمین شود.